Understanding Industrial Gear Lubes - Doug's Tip of the Month
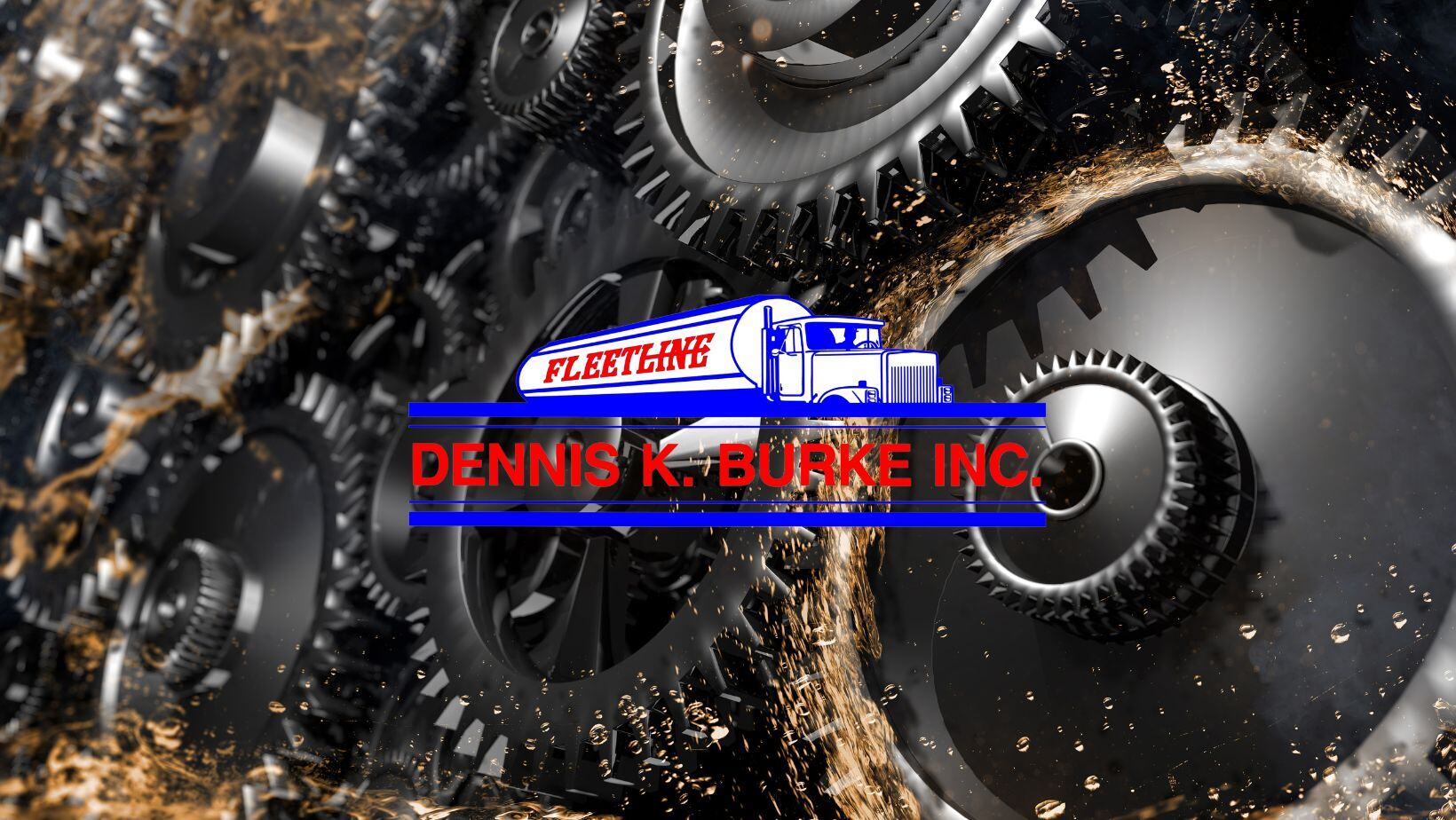
Industrial gear lubricants are essential to maintaining the efficiency and longevity of gearboxes across a wide range of industries. From reducing friction and heat to protecting against wear and corrosion, choosing the right gear lube ensures optimal equipment performance. In this blog, we’ll explore the three main categories of gear lubricants, their applications, benefits, and key factors to consider when selecting a lubricant, including special considerations for cold weather conditions.
The 3 Categories of Industrial Gear Lubricants
- R&O – normally used in operations with higher speeds, lower loads and no shock loading. Very limited additive that do not contain anti scuff (EP) or lubricity agents.
- EP also known as Anti-Scuff – normally used in operations with lower speeds, heavier loads and shock loading. Contain EP additives such as ZDDP or solids like Moly (molybdenum disulfide) or Graphite.
- Compounded – normally used in operations with sliding contact such as worm gears. Most commonly contain synthetic fatty acids for increased film strength.
Applications of Industrial Gear Lubes
- Industrial gear lubricants are used in gearboxes to control speed, torque, and direction. They are critical across various industries and equipment, including:
- Manufacturing – all types of manufacturing
- Conveyors, Crushers, Extruders
- Robotics
- Aerospace
- Machine tools
- Many more
- 6 Major Types of Gearboxes require specific Gear Lubes
- Helical
- Coaxial Helical Inline
- Bevel Helical
- Skew Bevel Helical
- Worm Reduction
- Planetary
Benefits of High-Quality Industrial Gear Lubes
Premium gear oils, such as Fleetline Industrial EP Gear Oil, P66 Extra Duty Gear Oil, Petro-Canada Enduratex Gear Oil, and Total Carter SH Gear Oil, provide several advantages:
- Longer Bearing Life
- Longer Seal Life
- Protection from Extreme Pressures
- Corrosive Protection
- Reduced Friction
- Remove Heat – Heat Transfer
- Improved Efficiency
Key Considerations when Choosing a Gear Lube
- OEM recommendations
- Viscosity – most important as determined by either the AGMA (American Gear Manufactures Association) and/or ANSI (American National Standards Institute).
- Additives – usually dictated by equipment needs and lubrication performance properties under normal operating conditions.
- Base Oil – Types can include Mineral, Synthetic, Esters and Glycols, etc.
Cold Weather Considerations for Gear Lubes
- Operating in colder climates introduces additional challenges. Consider these factors to protect your equipment:
- Ambient temperatures will affect the operating temperature of the equipment
- Gear Lubes with a higher VI (Viscosity Index) can operate in a much wider temperature range allowing it to Pour or Move better at colder temperatures while protecting at higher temperatures.
- Allowing Equipment to warm up to operating temperature slowly before operation with extend equipment and lubricant life.
- Ensuring the use of a quality gear lube with also aid in extending life, performance and efficient of the gearbox and bearings.
- Ambient temperatures will affect the operating temperature of the equipment
Industrial gear lubricants are the backbone of efficient and reliable gearbox operation. By understanding the different categories, applications, and considerations for gear lubes, you can select the best product to meet your equipment’s unique needs. Whether you’re operating in high-speed manufacturing environments or heavy-duty, shock-loaded applications, investing in quality gear lubricants will enhance performance, extend equipment life, and ensure long-term success.